Feintool wins a major customer in China's booming hydrogen economy. Together with the fuel cell manufacturer Feintool has developed a new generation of fuel cells. High volume production of metallic bipolar plates will start in Taicang in 2024.
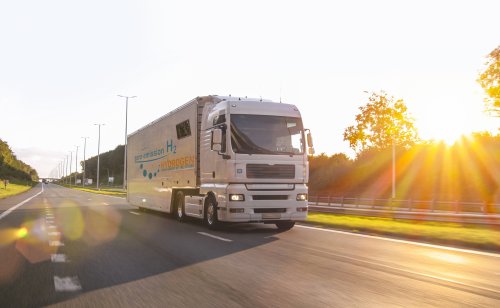
China is vigorously pushing ahead with the hydrogen economy and Feintool has emerged as one of the first European companies to establish a presence in this highly competitive market. The technology company has teamed up with a renowned Chinese manufacturer to develop a new generation of high-performance fuel cells.
In 2024, Feintool will ramp up the high volume production of metallic bipolar plates. These form the core of the fuel cells, which are mainly used in buses and commercial vehicles. This substantial order is anticipated to generate sales in the double-digit millions (CHF) over the next years.
“We are proud to have won a major customer in a market dominated by domestic players. We look forward to contributing to the decarbonization of China with our advanced production technology,” says Marcel Pernici, President of Feintool's parts business in Asia.
Feintool has a proven track record as a trusted development partner with the customer, which has six branches in China and supplies the country's leading bus and commercial vehicles manufacturers with fuel cell stacks. Feintool's engineering expertise and local presence in China were decisive in winning the contract, as Marcel Pernici explains: “This contract proves that Feintool successfully masters technology transfer on a global level and serves the Chinese market with highly efficient local-for-local solutions.”
The bipolar plates were developed at the Swiss site in Lyss, where prototypes will also be manufactured until October 2023. In collaboration with the German company SITEC two production lines have been established at the Taicang plant, near Shanghai, with a capacity of up to ten million bipolar plates per year. In a “shop-in-shop” concept, the laser specialist contributes machines and employees with expertise in laser welding, while Feintool manufactures the internal and external geometries of the bipolar plates using its FEINforming process on high-performance presses developed in-house. Thanks to this partnership, Feintool supplies customers with large-scale, ready-to-install, top-quality bipolar plates.
By the end of 2024, the substantial order is expected to run one production line at full capacity. As China's hydrogen economy is forecasted to experience robust growth by 2030 the manufacturer aims to gain further market share with the new fuel cell generation.
Building on their successful collaboration in Asia, SITEC and Feintool will continue their partnership manufacturing bipolar plates for fuel cells and electrolyzers in Europe.
For ready-to-install metallic bipolar plates: the joint competencies of Feintool and SITEC
FEINforming: Advantage through precision
FEINforming technology stands as a pivotal key to the future sustainability of fuel cells. The precise processing of ultra-thin material leads to a reduction in weight and volume, enabling a more compact arrangement of the fuel cells in the stack. An enhanced power density in the cell stack clears the way for high-performance and compact vehicle drives. Feintool provides a tailor-made, all-in-one solution for the production of optimized bipolar plates: presses specialized in bipolar plate production, FEM-optimized tool design, comprehensive engineering services as well as prototypes, pre-series, and series production.
FLEX Welding: Laser welding of the highest efficiency, process reliability and quality
The efficient operation of the laser in industrial production and the technological development of process-safe solutions are part of SITEC's core competencies. The laser works extremely fast, produces excellent weld seams and virtually distortion-free components. SITEC integrates lasers, welding optics and intelligent monitoring systems into automated production systems. For the production of metallic bipolar plates, the company relies on the specially developed FlexCell production system for needs-optimized production.